By Heather and Kendra Kastelan
For Energetics Engineer Heather, the morning of March 2 — test day — was more exciting than most. Alongside more than 20 Test and Research Operations teammates in Promontory, Utah, Heather dedicated weeks to preparing for the first static fire test of a new stage-one solid rocket motor that will be used on the Air Force’s LGM-35A Sentinel intercontinental ballistic missile. Sentinel represents a modernization of the ground-based leg of the U.S. strategic deterrent capability, replacing the Minuteman III system.
A static test safely ignites solid rocket motors, usually in a horizontal configuration, to gather critical data to ensure the motor meets design requirements. On test mornings, Test Conductor Heather — who joined Northrop Grumman in 2006 and was previously on active duty with the Air Force supporting static testing at the Utah Test and Training Range — guides the team through a detailed script that outlines procedures to execute the test, which is an industry standard across all static motor tests.
Here’s what Heather’s morning was like on the day of the first Sentinel static test:
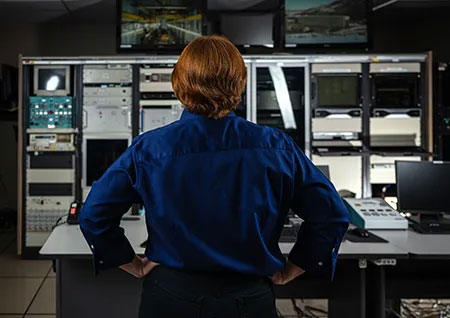
5 a.m. Time to get to work! I sat with my static test team in an underground, protected bunker at a safe distance from the Promontory test site. After I arrived in the control room, I stayed until the day was complete — my test day ritual — and stepped outside between tasks for fresh air and some sun. This allows me to be accessible to the team and watch the cameras strategically placed near the motor on TVs that surround the room.
6 a.m. The first dry run of the day, where our team went through every check and operation just as it should happen. I began my 60-minute script; each team member verbally confirmed their task was complete, and we did all but press the ignition button. This was our first opportunity to catch any glitches that may have surfaced overnight and allowed the team to grow even more familiar with the checklists that keep the team and our product safe.
7:30 a.m. With the dry run complete, I gave the go-ahead to prepare the motor. The team rolled open the door of the static test bay to expose it — a major milestone in the day. The motor sits above ground in a roofless U-shaped cement structure covered by a garage-like door that rolls back to expose the end and top of the motor. Sand was placed around the concrete test pad — which anchors the motor to the ground — and behind the motor’s nozzle to absorb the heat of the propellant during the test.
9 a.m. We executed another dry run, this time with the motor exposed and the test pad in a configuration as close to the real static test as we could get — giving a good indication of what the systems would see during the static test, such as ballistics, pressure and temperature. I ran through the verbal countdown script, this time testing the quench, an arm-like mechanism designed to shoot water into the motor’s nozzle to extinguish the remaining propellant post-fire. With the final dry run complete, the team grabbed an early lunch together before settling in for the test.
12 p.m. Just before the final countdown, I checked in with the program for the final go-ahead. With that, the test countdown started, and the static test areas were safely secured. Focusing on my checklist, I called on each team member one last time to confirm their systems were working and operations were complete.
12:59 p.m. In this final countdown, we felt confident and in control of everything, even the butterflies in our stomachs. 10… 9… 8… 7…
1 p.m. …1! The motor fired. Flames shot out of the test bay, just as planned. I watched the various camera angles knowing, moments later, those watching on-site, outside the bunker, would hear the roar and crackle. This was an intense moment of focus, but also of relief.
Once all the propellant inside the motor had burned, I called the quench sequence to extinguish the flame and preserve the motor. The test was complete.
These tests take months (or years) to prepare for, but it all comes down to a short sequence of events on test day. It’s mornings like these — as a member of the team that gets us to a safe and successful smoke and fire — when I’m most satisfied and proud of the work we do.